Key Strategies for Enhancing Warehouse Efficiency and Layout Optimization Guide
In modern warehouse management, layout design is directly tied to the operational efficiency of a business. A well-structured warehouse layout not only maximizes space utilization but also significantly boosts operational efficiency, reducing labor and equipment costs. However, many businesses still face challenges in warehouse layout and management. Today, Dongjian Racking will explore common issues in warehouse management and provide practical strategies for improving efficiency, helping businesses optimize their warehouse layout and enhance operational performance.
As market demands continue to evolve, businesses are required to manage an increasing variety and volume of products. Warehouses must not only handle a large number of SKUs (Stock Keeping Units) but also ensure fast and accurate classification, storage, and picking. This places higher demands on the flexibility and management of the warehouse system.
Rising Labor Costs
With labor costs on the rise, warehouse operational expenses are increasing as well. High-repetition tasks and intensive labor in the warehouse often lead to high employee turnover. To address this issue, warehouse managers must improve automation and optimize human resource allocation to reduce reliance on manual labor.
Pressure to Respond Quickly to Demands
Businesses face growing pressure to meet customers' demands for quick delivery. Warehouses must operate with greater speed and accuracy to ensure efficient order processing. This not only requires flexibility within the warehouse system but also tests the management of all operational stages.
Warehouse layout plays a crucial role in the storage and movement of goods. A well-designed layout not only maximizes space utilization but also reduces operational time, increasing overall work efficiency.
Process Optimization Principle: Ensure a smooth flow of goods from receiving, quality control, storage, picking, to shipping, minimizing unnecessary material handling and delays.
Maximizing Space Utilization: Use racks and equipment to fully utilize vertical space and maximize storage capacity.
Flexibility Principle: The layout should be flexible enough to adapt to changes in business needs and accommodate different types of goods and storage requirements.
Safety Principle: Ensure operational safety within the warehouse by setting appropriate aisle widths and emergency exits, safeguarding both personnel and equipment.

2. Choosing and Configuring Racks
Racking systems are the backbone of warehouse layouts. Proper rack selection and configuration can greatly improve storage efficiency and operational convenience. Depending on the weight, size, and storage needs of goods, choosing the right type of rack is essential:
Heavy-duty racks: Suitable for storing large or heavy items, offering high storage density. They are ideal for palletized goods but require the use of forklifts.
Medium-duty racks: Suitable for medium-weight goods, offering great flexibility. They are ideal for areas where manual handling is required and provide ample storage space.
Light-duty racks: Ideal for storing lightweight, small items, often used in retail or small-scale warehouses. They are easy to operate and maximize space utilization.

3. Optimizing Workflow Design
Workflow design refers to the movement paths of goods and personnel within the warehouse. By optimizing these paths, operational time can be reduced, improving overall efficiency:
Shortest Path Principle: Design the shortest possible path from receiving to shipping, minimizing unnecessary handling and waiting times.
Clear Zoning: Divide the warehouse into clear zones such as receiving, storage, picking, packaging, and shipping areas, ensuring smooth operations.
Avoiding Cross-interference: Ensure that goods flow is not disrupted by different workflows, reducing interference between personnel and equipment.
Optimizing Aisle Widths: Design aisle widths based on the actual size of goods and equipment, ensuring easy operation while maximizing storage space.

4. Optimizing Storage and Picking Zones
Properly planning the storage and picking zones can significantly enhance picking efficiency:
Allocate Goods by Picking Frequency: Distribute goods based on their picking frequency. High-frequency items should be stored near the picking area, while low-frequency items can be placed further away.
Dynamic Layout Adjustments: Regularly analyze picking and inventory data to dynamically adjust storage and picking zone configurations, ensuring the efficient use of space and resources.

Follow Dongjian Racking for more practical tips on warehouse management, and let us help you optimize your operations and boost competitiveness!
Disclaimer: Some images are sourced from the internet. If any infringement occurs, please notify us, and we will promptly remove them.
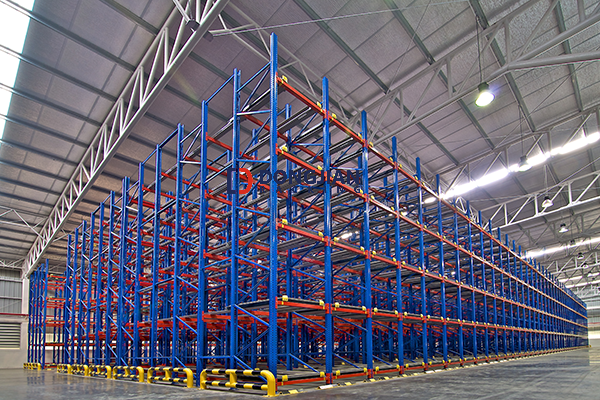
The Three Main Challenges Facing Warehouse Departments
Diverse Inventory ManagementAs market demands continue to evolve, businesses are required to manage an increasing variety and volume of products. Warehouses must not only handle a large number of SKUs (Stock Keeping Units) but also ensure fast and accurate classification, storage, and picking. This places higher demands on the flexibility and management of the warehouse system.
Rising Labor Costs
With labor costs on the rise, warehouse operational expenses are increasing as well. High-repetition tasks and intensive labor in the warehouse often lead to high employee turnover. To address this issue, warehouse managers must improve automation and optimize human resource allocation to reduce reliance on manual labor.
Pressure to Respond Quickly to Demands
Businesses face growing pressure to meet customers' demands for quick delivery. Warehouses must operate with greater speed and accuracy to ensure efficient order processing. This not only requires flexibility within the warehouse system but also tests the management of all operational stages.

The Concept and Importance of Warehouse Efficiency
Warehouse efficiency refers to optimizing resource allocation and operational processes to achieve maximum efficiency and customer satisfaction at the lowest cost. In modern supply chain management, warehouse efficiency is a key indicator of a company's logistics capabilities. It involves multiple factors such as inventory management, warehouse layout, and personnel management. Optimizing these elements can significantly improve warehouse efficiency and, in turn, enhance the business's competitiveness.
Key Strategies for Enhancing Warehouse Efficiency
1. Warehouse Layout OptimizationWarehouse layout plays a crucial role in the storage and movement of goods. A well-designed layout not only maximizes space utilization but also reduces operational time, increasing overall work efficiency.
Process Optimization Principle: Ensure a smooth flow of goods from receiving, quality control, storage, picking, to shipping, minimizing unnecessary material handling and delays.
Maximizing Space Utilization: Use racks and equipment to fully utilize vertical space and maximize storage capacity.
Flexibility Principle: The layout should be flexible enough to adapt to changes in business needs and accommodate different types of goods and storage requirements.
Safety Principle: Ensure operational safety within the warehouse by setting appropriate aisle widths and emergency exits, safeguarding both personnel and equipment.

2. Choosing and Configuring Racks
Racking systems are the backbone of warehouse layouts. Proper rack selection and configuration can greatly improve storage efficiency and operational convenience. Depending on the weight, size, and storage needs of goods, choosing the right type of rack is essential:
Heavy-duty racks: Suitable for storing large or heavy items, offering high storage density. They are ideal for palletized goods but require the use of forklifts.
Medium-duty racks: Suitable for medium-weight goods, offering great flexibility. They are ideal for areas where manual handling is required and provide ample storage space.
Light-duty racks: Ideal for storing lightweight, small items, often used in retail or small-scale warehouses. They are easy to operate and maximize space utilization.

3. Optimizing Workflow Design
Workflow design refers to the movement paths of goods and personnel within the warehouse. By optimizing these paths, operational time can be reduced, improving overall efficiency:
Shortest Path Principle: Design the shortest possible path from receiving to shipping, minimizing unnecessary handling and waiting times.
Clear Zoning: Divide the warehouse into clear zones such as receiving, storage, picking, packaging, and shipping areas, ensuring smooth operations.
Avoiding Cross-interference: Ensure that goods flow is not disrupted by different workflows, reducing interference between personnel and equipment.
Optimizing Aisle Widths: Design aisle widths based on the actual size of goods and equipment, ensuring easy operation while maximizing storage space.

4. Optimizing Storage and Picking Zones
Properly planning the storage and picking zones can significantly enhance picking efficiency:
Allocate Goods by Picking Frequency: Distribute goods based on their picking frequency. High-frequency items should be stored near the picking area, while low-frequency items can be placed further away.
Dynamic Layout Adjustments: Regularly analyze picking and inventory data to dynamically adjust storage and picking zone configurations, ensuring the efficient use of space and resources.

Conclusion
Warehouse management is a critical part of supply chain operations. By optimizing warehouse layouts, selecting the right racking systems, improving workflow design, and efficiently organizing storage and picking zones, businesses can significantly enhance warehouse efficiency and reduce operational costs. With extensive industry experience, Dongjian Racking offers customized, efficient storage solutions to help businesses tackle the challenges of warehouse management.
Follow Dongjian Racking for more practical tips on warehouse management, and let us help you optimize your operations and boost competitiveness!
Disclaimer: Some images are sourced from the internet. If any infringement occurs, please notify us, and we will promptly remove them.